La maintenance prédictive : anticiper pour optimiser
Dans un monde industriel en constante évolution, la maintenance est passée d’une approche réactive (réparer après la panne) à une approche proactive (prévenir la panne). Parmi les différentes stratégies de maintenance proactive, la maintenance prédictive se distingue par son utilisation de données et de technologies avancées pour anticiper les défaillances et optimiser les interventions. Cet article explore en détail ce qu’est la maintenance prédictive, son fonctionnement, ses avantages et les étapes clés pour sa mise en œuvre.
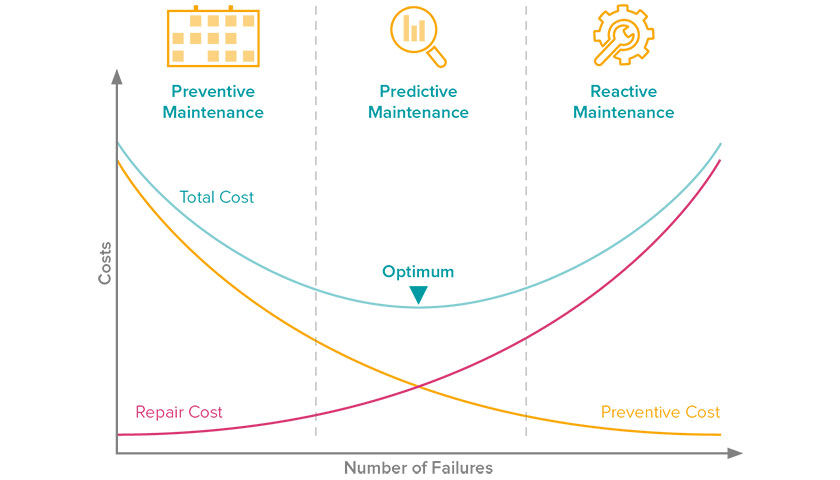
Qu’est-ce que la maintenance prédictive ?
La maintenance prédictive, parfois appelée maintenance prévisionnelle, est une approche de maintenance qui utilise des données et des techniques d’analyse pour prédire le moment où un équipement est susceptible de tomber en panne. Contrairement à la maintenance corrective (réparation après la panne) ou à la maintenance préventive (interventions planifiées à intervalles réguliers), la maintenance prédictive vise à intervenir avant la défaillance, en se basant sur l’état réel de l’équipement.
Comment fonctionne la maintenance prédictive ?
La maintenance prédictive repose sur la collecte et l’analyse de données provenant de diverses sources :
- Capteurs : Des capteurs installés sur les équipements mesurent en continu des paramètres tels que la température, les vibrations, la pression, le niveau d’huile, les ultrasons, les émissions acoustiques, le courant électrique, etc.
- Systèmes de surveillance : Ces systèmes collectent et enregistrent les données des capteurs.
- Logiciels d’analyse : Des algorithmes d’analyse de données, d’apprentissage automatique (machine learning) et d’intelligence artificielle (IA) sont utilisés pour identifier des tendances, des anomalies et des signes avant-coureurs de défaillance.
- Historique de maintenance : Les données des interventions de maintenance passées sont également prises en compte pour affiner les prédictions.
L’analyse de ces données permet de :
- Détecter les anomalies : Identifier les écarts par rapport au fonctionnement normal de l’équipement.
- Prévoir les défaillances : Estimer la probabilité et le moment d’une future panne.
- Optimiser les interventions : Planifier les opérations de maintenance au moment optimal, en évitant les arrêts imprévus et en maximisant la durée de vie des équipements.
Les avantages de la maintenance prédictive
- Réduction des arrêts de production non planifiés : En anticipant les pannes, la maintenance prédictive minimise les interruptions de production et les pertes financières associées.
- Optimisation des coûts de maintenance : En intervenant uniquement lorsque c’est nécessaire, on réduit les coûts liés aux interventions inutiles et au remplacement prématuré des pièces.
- Amélioration de la sécurité : En prévenant les défaillances, on réduit les risques d’accidents et d’incidents liés aux pannes d’équipement.
- Prolongation de la durée de vie des équipements : En maintenant les équipements en bon état de fonctionnement, on prolonge leur durée de vie et on optimise leur retour sur investissement.
- Amélioration de la qualité des produits : En évitant les arrêts et les dysfonctionnements, on assure une production plus stable et une meilleure qualité des produits.
Les étapes clés pour la mise en œuvre de la maintenance prédictive
- Identifier les équipements critiques : Prioriser les équipements dont la défaillance aurait un impact majeur sur la production ou la sécurité.
- Définir les paramètres à surveiller : Choisir les paramètres pertinents à mesurer en fonction du type d’équipement et des modes de défaillance possibles.
- Installer les capteurs et les systèmes de surveillance : Mettre en place les outils de collecte et d’enregistrement des données.
- Choisir les outils d’analyse : Sélectionner les logiciels et les algorithmes d’analyse les plus adaptés aux besoins.
- Former le personnel : Former les équipes de maintenance à l’utilisation des outils et à l’interprétation des données.
- Mettre en place un processus d’amélioration continue : Ajuster et optimiser le système de maintenance prédictive en fonction des retours d’expérience et des nouvelles données.
Les technologies utilisées en maintenance prédictive
- Analyse vibratoire : Mesure et analyse les vibrations des machines tournantes pour détecter les déséquilibres, les défauts d’alignement, les problèmes de roulements, etc.
- Thermographie infrarouge : Utilise des caméras thermiques pour détecter les anomalies de température qui peuvent indiquer des problèmes électriques, mécaniques ou d’isolation.
- Analyse des huiles : Analyse les propriétés des huiles de lubrification pour détecter la présence de contaminants, l’usure des composants et la dégradation de l’huile.
- Ultrasons : Utilise les ondes ultrasonores pour détecter les fuites, les défauts d’étanchéité, les décharges électriques partielles, etc.
- Analyse des données et Machine Learning : Utilise des algorithmes pour identifier des corrélations et des tendances dans les données et prédire les défaillances.
La maintenance prédictive représente une avancée majeure dans le domaine de la maintenance industrielle. En utilisant les données et les technologies d’analyse, elle permet d’anticiper les pannes, d’optimiser les interventions et d’améliorer la performance globale des installations. Bien que sa mise en œuvre nécessite un investissement initial, les avantages à long terme en termes de réduction des coûts, d’amélioration de la sécurité et d’augmentation de la productivité en font une stratégie de maintenance de plus en plus adoptée par les entreprises.